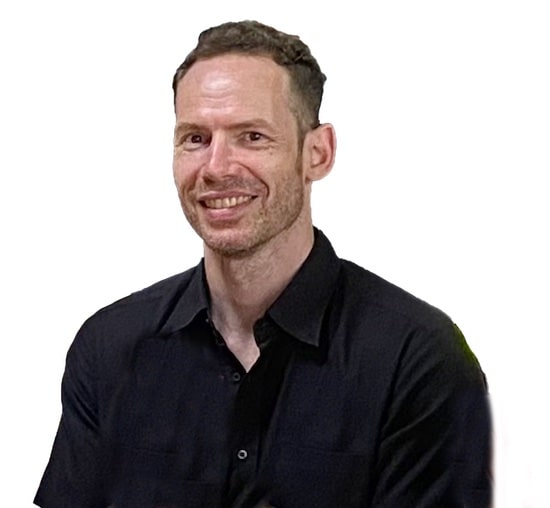
Author of this article: Tim Wolput
Former Fujitsu and Toyota veteran Toru Takagi Sensei and Yokahama National University Associate Professor Kodo Yokozawa have been conducting research on the effectiveness of a new breed of Toyota way Management System called Woven Work Design. It prominently features Obeya and helps organizations develop towards a culture of autonomous management[1].
We will share with you some preliminary results of the effects of a shift to Obeya-based management within the Woven Work Design structure.
First, a bit of Obeya history: the rise of Obeya and its key players
About 57 years ago, Mr. Toshio Horikiri (Founder and CEO of Toyota Engineering Corporation, TEC for short) joined Toyota Motor Corporation, where he learned and experienced several practices that were to become part of his DNA. Among them and definitely one of the most essential ones, was Obeya – back then used particularly for new product development[2]. After retiring from Toyota in 2002, Horikiri established the TPS consulting firm, Toyota Engineering Corporation and integrated his experience into a system called Total-TPS. An essential part of this system covered in a detailed way how Toyota was able to develop new models faster than any other car manufacturer through simultaneous engineering, upstream Kaizen, and a practice of visual management, i.e. Obeya[3]. Later, in 2008 the ideas of Total-TPS were extended to be applied throughout the whole organization, thus giving birth to the Toyota way Management System (TMS)[4], described by Takashi Tanaka in the YouTube videos that popularized Obeya in the West.
To understand how this ball got rolling in the West, we must go back to the early 2000s when Harley Davidson was struggling with its new product development. Lean or TPS had already proven its value to make production more efficient, but there had not yet been many successes of ‘people taking improvement tools from physical work and trying to apply them to people doing intellectual work, specifically in knowledge work, executive strategy, engineering, IT, and finance’[5]. At that time Obeya was still largely unknown in the West, whereas at Toyota it was already common practice in the 1990s and even before[6].
To make a long story short, Prof. Alan Ward of MIT introduced Takashi Tanaka to Harley Davidson. Tanaka then brought in Toyota Engineering Corporation CEO, Toshio Horikiri to help Don Kieffer of Harley Davidson develop engines, and later new motorcycle models, faster and better, using the Obeya methodology[7]. This was one of the first times that Obeya was successfully applied by a western company.
In 2006 we see the beginning of another story of a western early adopter of Obeya: Boeing. Around that time Sharon Tanner joined the Boeing Product Development organization trying to get grips on how to bring lean into product development. In 2007 they also decided to bring in Takashi Tanaka[8], who again teamed up with the experts at Toyota Engineering Corporation to help with the product development challenges at that time. TEC sent Toshio Horikiri and a former Fujitsu and Toyota man called Toru Takagi (remember that name). And guess what they came up with to pull Boeing out of the slums? You’ve guessed it already: Obeya[9].
The Western world owes a lot to Takashi Tanaka’s efforts to introduce Obeya in the West, but we should not forget that we would not be here today without the wisdom and expertise of true Obeya sensei like Toshio Horikiri and Toru Takagi.
The latter, Toru Takagi, is currently taking the Toyota Way Management System to another level.
Toru Takagi introduces Woven Work Design: a new style Toyota way Management System
Have you ever heard of Woven Work Design? My guess is not, but recently in Japan, Woven Work Design is gaining attention as a newly evolving version of the Toyota way Management System[10]. With a strong focus on people, it strives to help employees do meaningful work and not let them waste, what is most valuable to us humans, time, by having to do meaningless tasks. You may know this as MUDA.
I learned this the hard way from Toru Takagi, who is currently CEO of the IT Management Institute. When Mr. Takagi and I were in Houston for the Lean Summit in 2019, I mentioned to him during dinner that in a weird way, MUDA could be considered as a positive thing as it allows us to continuously improve. He stared at me hard and said: ’Tim you haven’t understood anything about MUDA!’ He then went on to say that a leader should never allow MUDA to exist in the workplace. Asking your people to do tasks that add no value at all is like throwing away a part of their lives, you are stealing what is most precious and can never be won back: time.
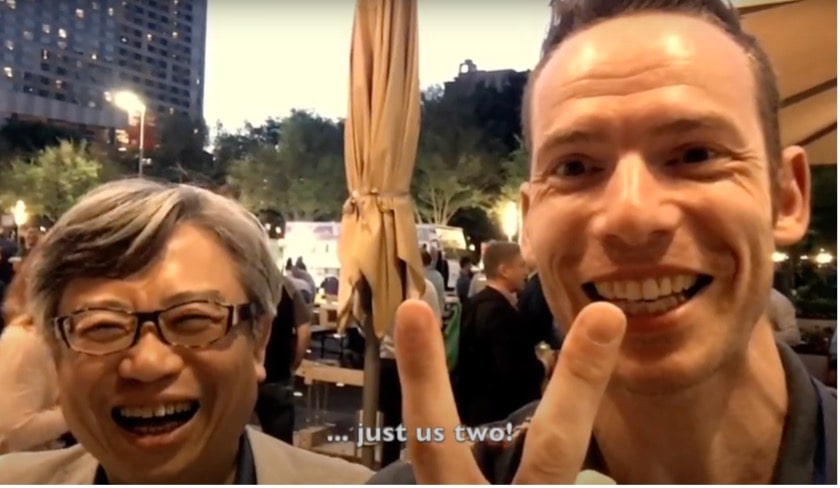
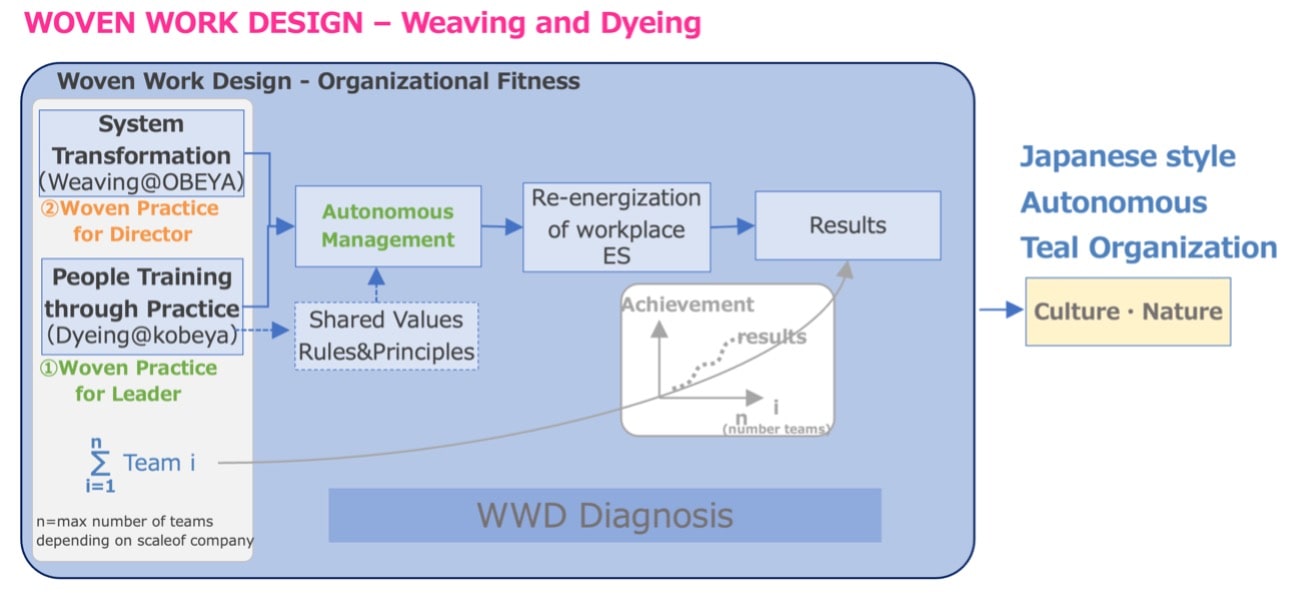
With Woven Work Design we try to get rid of coercive control-management and create a shift to autonomous management that helps people get results, experience fulfilment, and realize personal growth through the work that they are doing. Visual management plays an extremely important role in this process, in particular the idea of Obeya and Kobeya[11].
Autonomous work design with Obeya creates engagement
With the help of Yokohama National University Associate Professor Kodo Yokozawa, we started research in 2022 in which we surveyed two Japanese companies to investigate how well they were able to perform value added work[12]. Simply put, we looked at work dividing it into 3 categories: Net Work, Indirect Work and Waste. We call these the 3 work elements.
Net Work is value-added work. Indirect Work is something you need to do to be able to do Net Work. Waste consists of totally meaningless activities.
An easy example:
- The barber cuts hair = net work
- The barber takes his scissors = indirect work
- The barber drops his scissors = waste
To measure the work elements ratio we used what is called a 5 min scan in which we plotted for multiple days the daily ratios of the 3 work elements. We found the following:
- Company S on average was doing 40.7% Net Work, 53.4% Indirect Work and 5.9% Waste.
- Company F on average was doing 20.9% Net Work, 70.8% Indirect Work and 8.3% Waste.
- Interestingly Company S was a Toyota-related group, hence their relatively high percentage of Net Work.
Still, we see that the biggest lump of what we do every day doesn’t consist of net work, nor waste, but indirect work.
To some surprisingly, our findings suggested that what is holding us back from doing more value-added work is not so much Waste, but indirect work. Put differently, even if you eliminate MUDA, you’re still stuck with a lot of indirect work. We call this indirect work ‘The Swamp’ because it prevents us from moving forward smoothly.
Our next step was clear. We needed to know what this swamp consists of. We found the following:
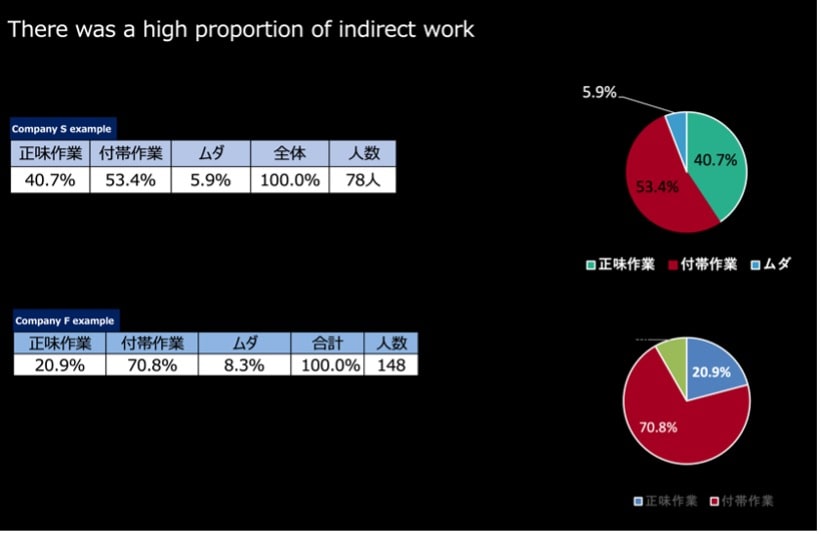
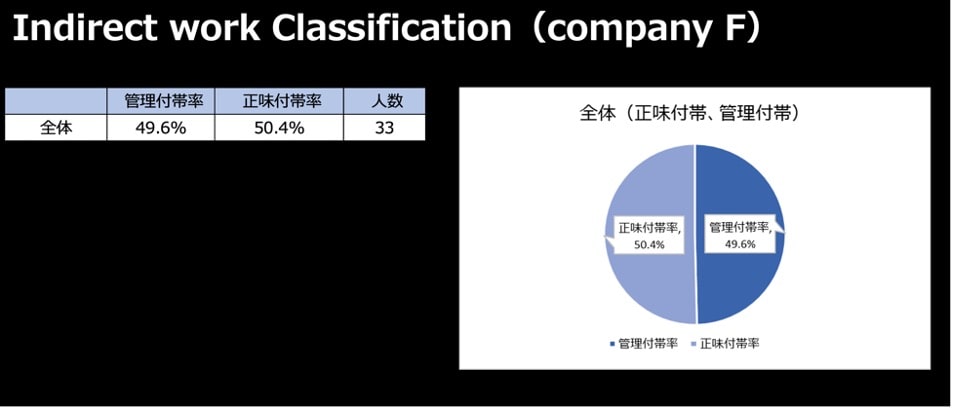
About 50.4% of the indirect work was directly related to net work, i.e. preparation and arrangement of net work. The remaining 49.6% consisted of control-management related tasks: reporting, consulting, meeting room meetings, getting permissions, …
So, about half of the indirect work consists of what Paul S. Adler (Professor of Management and Organization, Sociology, and Environmental Studies at the University of Southern California) would call coercive bureaucracy related elements[13]. These types of organizations rely on conventional top-down management in which the idea of Obeya is entirely absent.
We can see that control-management is significantly hindering the performance of organizations. People don’t get anything done because they get buried in control-management. To get rid of control-management Woven Work Design proposes a shift to a structure that enables people to work together in autonomous teams, or as Paul S. Adler calls it: an enabling bureaucracy. Here, visual management (Obeya and Kobeya) plays an essential role as it helps teams to see the why, what and how of the work and hence helps in creating the circumstances in which people can think, decide, act and cooperate by themselves without having to be ordered to do stuff.
The proof of the pudding however is in the eating, so we decided to investigate further what the shift to Obeya and Kobeya style autonomous management at Company F brought forth.
This is what we found:
Before introduction of WWD Obeya and Kobeya style working
During 2022, as shown above the first stage of the research suggested that a coercive bureaucracy causes high volume of indirect work which in turn negatively impacts engagement, enthusiasm and vitality of employees. This was confirmed when we measured employee engagement factors and found them to be low.
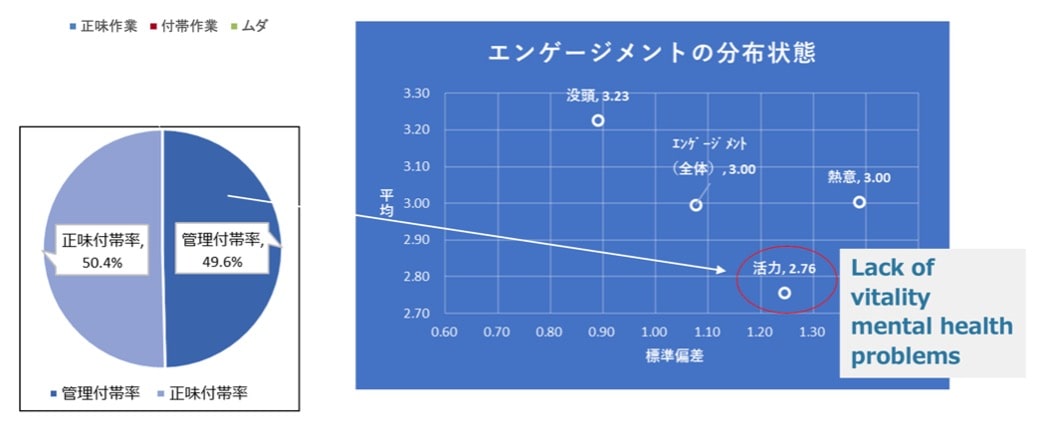
After introducing WWD Obeya and Kobeya style working
Then a shift to autonomous management based on Woven Work Design was introduced into the organization using Obeya to transform the organizational structure (weaving) and Kobeya to develop the employees (dyeing). The organization started to evolve to autonomous teams employing Obeya and Kobeya. In the first half of 2023, employee engagement was again measured, and we found a significant improvement of engagement, vitality, and enthusiasm among employees.

Conclusion
Truth be told, we are not yet seeing the full impact on the amount of indirect work. However, the journey has only just begun. As company F evolves from a coercive bureaucracy into a more enabling bureaucracy actively using Obeya and Kobeya, we expect the percentage of control-management related indirect work to drop significantly.
The results thus far are more than promising: we now know for certain that Obeya and Kobeya as essential elements of Woven Work Design engage people more and create high vitality and enthusiasm within the organization. We are convinced that this will also have a strong impact on the fitness of the company. As Takagi sensei explains it: ‘We develop the people in the Kobeya and we transform the organization as we weave the system in the Obeya.’
Goodbye reports, goodbye meeting room meetings, and get stuff done: let’s go Obeya!
References
- [1] We will elaborate on Woven Work Design during the Obeya Summit.
- [2] Horikiri Toshio, “Cost” The Toyota Way, Tokyo, Kanki Publishing, 2016
- [3] Hoek, Koopmans, Wolput, Horikiri, Lean Productie Systeem, Amsterdam, Boom Uitgevers, 2021
- [4] Hoek, Koopmans, Wokput, Horikiri, Lean Management Systeem, Amsterdam, Boom uitgevers, 2020
- [5] Orlowski, Naik, Kieffer, Drive an Oracle Implementation On Time and On Budget with Visual Management Methodology , 2017, p.5 (http://shiftgear.work/wp-content/uploads/2017/07/white-paper_vm_for_oracle_oaug_collaborate17.pdf)
- [6] As explained by Horikiri during a conversation in 2017 at the HQ of TEC in Nagoya. I distinctly remember Horikiri telling me that when he just started consulting in 2002, much to his surprise there seemed to be no Western companies that had ever heard of Obeya, while it was considered common practice at Toyota.
- [7] Ward A.,Oosterwal, D.P., Sobek II, D.K., Visible Knowledge for Flawless Designs: The Secret behind Lean Product Development, NY, Taylor & Francis Group, 2018
Oosterwal, D. P.,The lean machine : how Harley-Davidson drove top-line growth and profitability with revolutionary lean product development, NY, AMACOM, 2010 - [8] Tanner Sharon, Lean Summit 2010 – Lean for Leaders in the Executive Office, https://www.youtube.com/watch?v=RX2LrSKkiu0&t=1510s
- [9] Horikiri Toshio, “Cost” The Toyota Way, Tokyo, Kanki Publishing, 2016
- [10] Takagi Toru, Sankai Kazutaka, Woven Practice for Leader, 株式会社インプレスR&D
POD 出版サービス, 2021 - [11] Kobeya refers to Gemba level smaller scale Obeya
- [12] This research was conducted by WWD Organization Management Study Group (WWD組織マネジメント研究会) under guidance of Yokohama National University Associate Professor Kodo Yokozawa and IT-Management CEO Toru Takagi. Findings, data and visuals subject to copyright ©︎ 2020-2023 IT Management Institute LLC All Rights Reserved.
- [13] Adler Paul S, Borys Bryan, Two types of bureaucracy: Enabling and coercive in Administrative Science Quarterly; Mar 1996; 41, 1; ABI/INFORM Global https://www.researchgate.net/publication/200552237_Two_Types_of_Bureaucracy_Enabling_and_Coercive