Streamlining processes for efficiency
Lean Management is a philosphy that roots from the Toyota Production System as developed by Taiichi Ohno, Shigeo Shingo since the late 1940s. Lean management is about continuously improving work processes, purposes, and people. With the aim to maximize customer value while minimizing waste. Lean can be applied in any business and process, be it production or service. In essence, Lean is a way of thinking and acting, not a cost reduction programme or a mere set of tools.
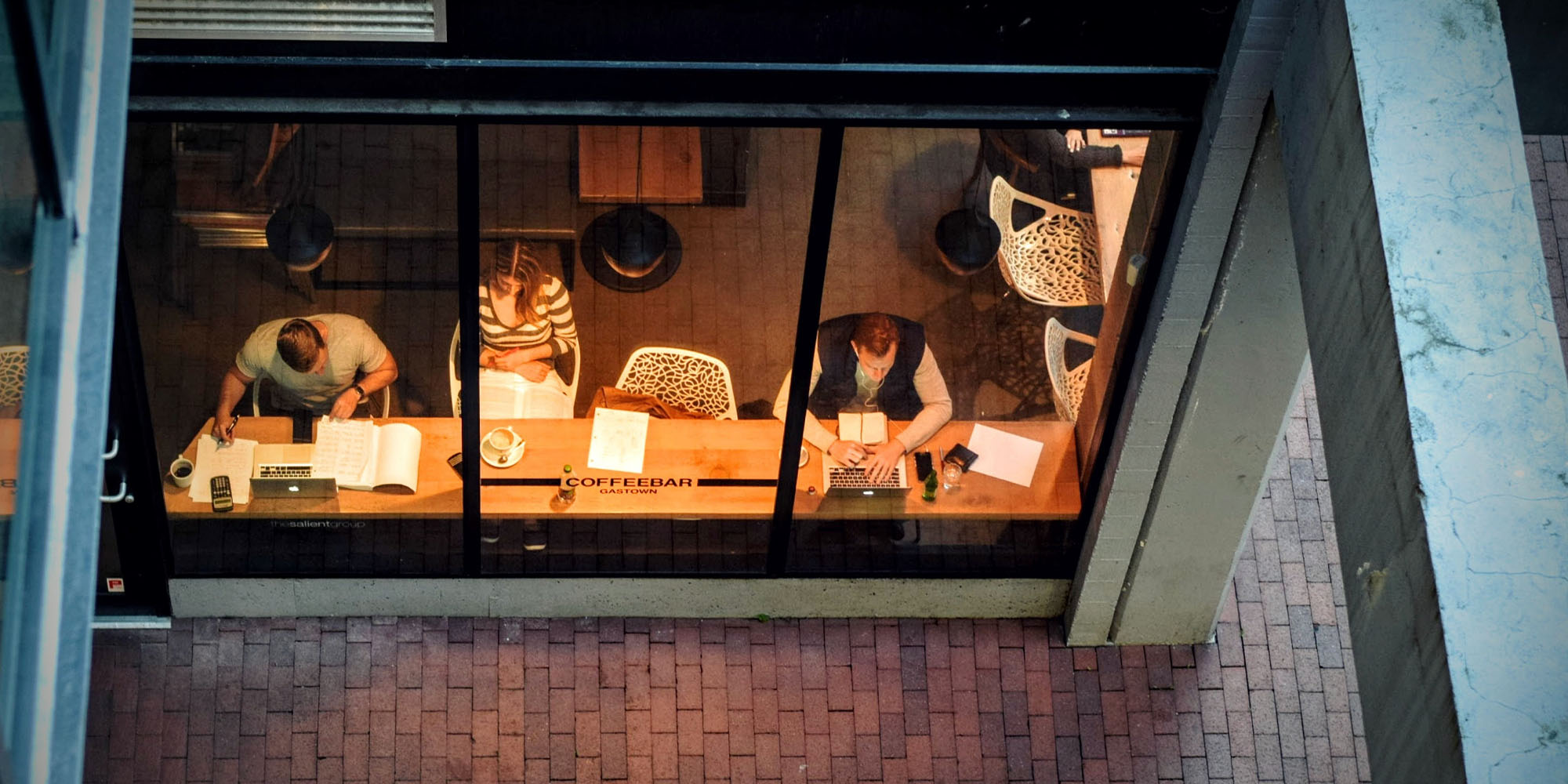
Lean thinking over time
Lean manufacturing
The story of Lean starts in the 1940s and has its roots in the Toyota Production System. Ever since, lean management has helped create value all around the world in various industries, governments and non-governments. The Toyota Production System, originally called “just-in-time production”, builds on the approach created by the founder of Toyota, Sakichi Toyoda. The principles underlying the TPS are embodied in The Toyota Way.
The term ‘Lean’ was made up by John Krafcik in his 1988 article “Triumph of the Lean Production System”. Later on in 1996, ‘Lean’ was further defined by James Womack and Daniel Jones, founders of the Lean Enterprise Institute and authors of the book “Lean Thinking”.
Ever since, Lean thinking has spread across the world and evolved to five basic principles of Lean management.
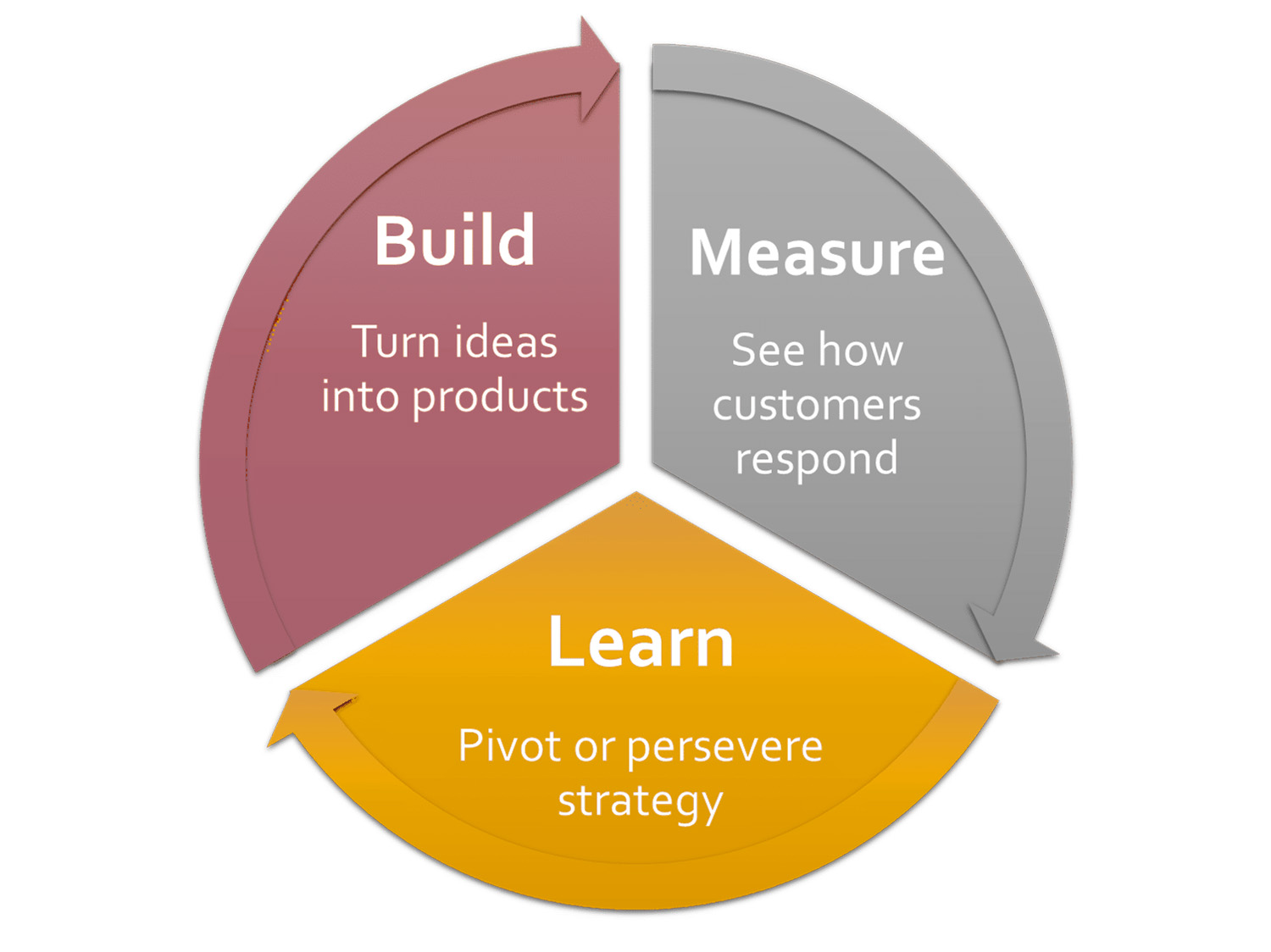
The lean startup
Eric Ries, an engineer, and serial entrepreneur developed a methodology based on the Lean principles to help startups succeed. In 2011, he packed his ideas in a book called “The Lean Startup”. The concept consists of 5 basic principles that aim to help startups be more flexible and responsive to changes.
Inspired by lessons from lean manufacturing, the Lean Startup Methodology relies on “validated learning,” rapid scientific experimentation, as well as a number of counter-intuitive practices that shorten product development cycles, measure actual progress without resorting to vanity metrics, and learn what customers really want.
Obeya in lean practices
Obeya or Oobeya (from Japanese Ōbeya 大部屋 “large room”) stems from the 90’s when Toyota was building the Prius. During the development of the Prius all individuals involved met in the Obeya to speed communication and decision-making. Ever since, it is considered to be a Lean Practice. However in the past years Obeya has also been applied for scaling business agility.
Read more about Obeya here
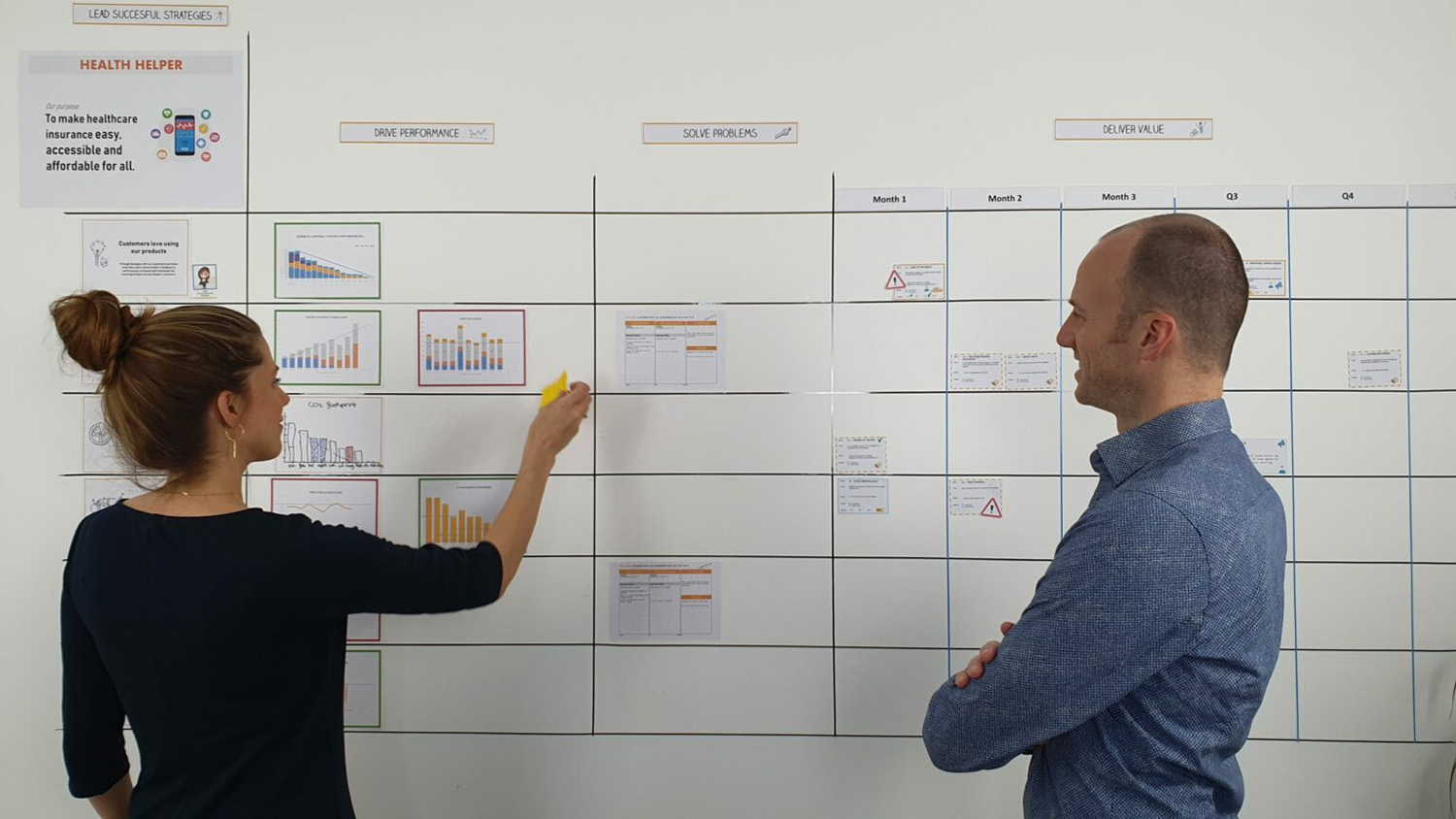