What are the 5 Principles of Lean?
The five Lean Principles have been defined by Womack and Jones in their book “The Machine That Changed the World”.
These principles of Lean Manufacturing consist of a five-step thought process for guiding the implementation of lean using lean methodology.
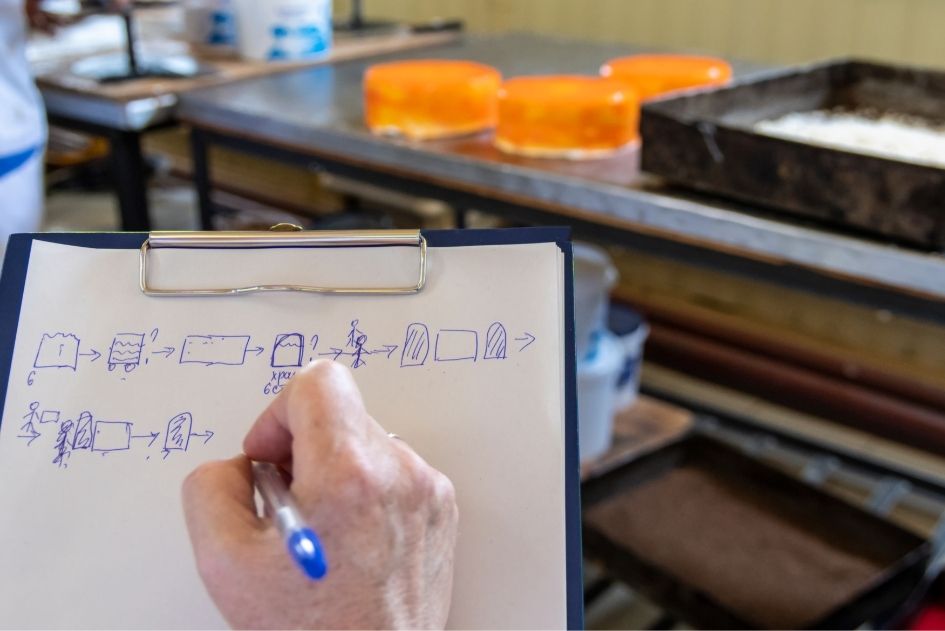
1. Identify Value
Every company exists because of its customers. The question that every company should always ask itself is: How can we create most value for our customer? Value is a process or service (or parts of it) that the customer wants to pay for or wait for. In order to know what value is for our customer, we first need to know who our customer is (this can also be internal departments or colleagues) and where the customer derive value from.
Keep in mind that customer value is different from customer demand. Successful companies understand so well what valuable is for their (potential) customers, that they surprise their customers with a product or service that they have not yet asked for, but which proves to be of great value.
2. Value Stream Mapping
After specifying what is of value to the customer, it is important to distinguish which activities within the company add value for the customer and which do not. One way to gain insight into how Value is created is Value Stream Mapping.
Value Stream Mapping is a Lean Methodology that visualizes all steps in a Value Stream from creation to delivery iof the product, service and/or experience the customer desires. Learn more about Value Stream Mapping here.
3. Create Continuous Workflow
The next principle is all about creating ‘flow’ by removing all identified waste, leaving only value adding activities. Think for example of creating unnecessary stock or waiting. Then coordinate these activities so that there are no bottle necks and a natural flow is created.
Just as water flows freely downstream, the value chain should experience a smooth progression from start to finish. The purpose of ‘flow’ is to let the service or product “flow” to the customer according to the quality requirements of the customer without losing time. Maintaining flow requires careful synchronization of each activity from origin to delivery.
4. Create a Pull System
Now that the waste within the business process has been minimized and everything is focused on adding value to the customer, it is only useful to actually produce if the customer asks for it. This principle is called “Pull”: only do what is necessary, when it is necessary. This limits unnecessary intermediate and final stocks.
5. Seek Perfection
The fifth principle within Lean is the pursuit of perfection by continuous improvement. The goal is to be a learning organization that improves step by step every day instead of spearheading a big improvement project every now and then. There is always room for improvement in lean organizations.